Влияние мощности УШМ на производительность при шлифовании.
28 июня 2021 — 11:48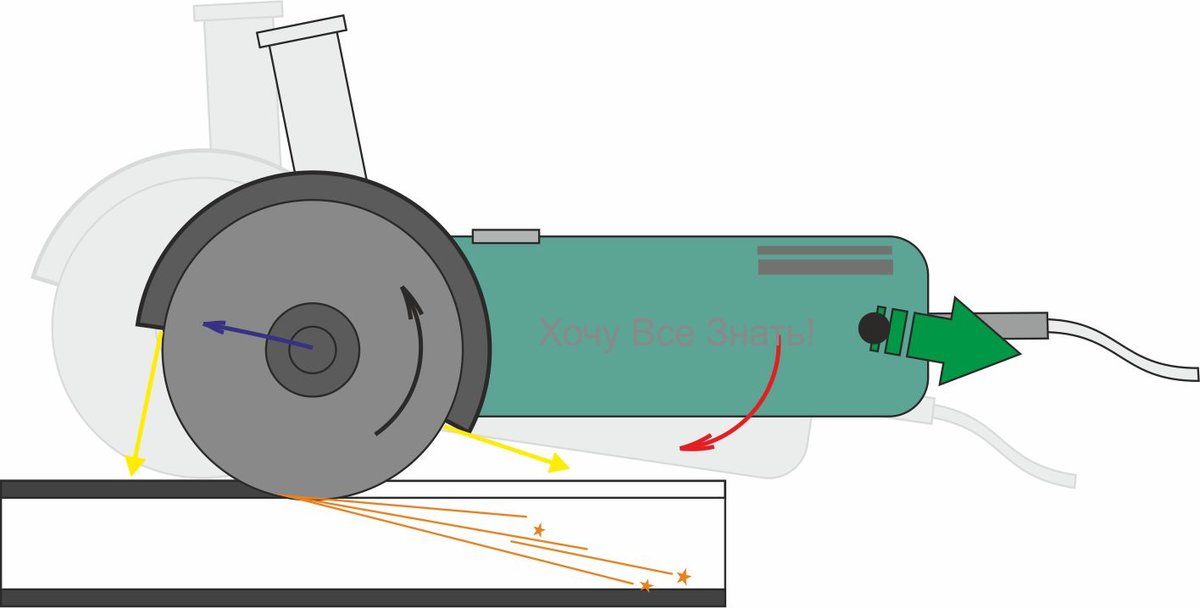
Попытки объяснить, что маломощный инструмент не годится для шлифовки, наталкиваются на откровенное непонимание: ведь УШМ – это же углошлифовальная машина, не так ли? Чем меньше мощность, тем дешевле инструмент, и вроде бы можно сэкономить довольно приличную сумму. Пусть даже работа займёт больше времени – этими потерями очень часто готовы пожертвовать.
Мы тестируем абразивы уже не первый год, причём не все наши тесты находят отражение в публикациях. Иногда это предварительные испытания, иногда мы проводим их по заказу компаний для внутреннего использования. Поэтому сталкивались с разными ситуациями, и как влияет мощность УШМ на скорость работы, знаем не понаслышке. Однако недостаточно просто написать: «Экономия выйдет вам боком». Будем считать, что это теорема и она требует доказательств. Вот в этой статье мы их и приведём.
НА КОГО РАССЧИТАНА СТАТЬЯ?
Эта статья будет интересна весьма широкой аудитории. Например, специалистам по материально-техническому обеспечению и снабжению промышленных предприятий. Теоретически они и так должны разбираться в этом вопросе, потому что обязаны предлагать обоснованные решения о покупке того или иного вида инструментов и оснастки. Но регулярные случаи использования откровенно неподходящих для поставленных задач УШМ говорят о том, что или такие сотрудники есть не везде, или они не всегда утруждают себя подобными расчётами.
Руководству предприятий эта информация тоже будет крайне полезна – мы предлагаем простую и понятную методику, которая поможет проконтролировать эффективность работы отдела снабжения. Теперь и сами посчитаете, в какие суммы вашему предприятию обходится неграмотный выбор.
Продавцам электроинструмента также настоятельно рекомендуем внимательно изучить этот материал – здесь есть отличные аргументы для рекламы именно мощных и, соответственно, более дорогих инструментов. Причём аргументы вполне разумные, ни о каком «впаривании» речь не идёт – вы просто сможете объяснить покупателю, что ему, действительно, нужна модель более высокого класса, и экономия не пойдёт на пользу.
ОТБОР УЧАСТНИКОВ И МЕТОДИКА ТЕСТА
Условия проведения испытаний предельно просты и могут быть легко воспроизведены каждым, кто захочет проверить наши выкладки. На этот раз мы сознательно ограничились ручной шлифовкой, нам нужно было воспроизвести обычную рабочую ситуацию, в которой эксплуатируются обдирочные абразивы. И кроме того, это ведь не тест самих кругов, хотя если вы нам полностью доверяете, то можете считать наши испытания тестом. Работал один человек, он же – один из авторов статьи. Сравнивая полученные в этот раз результаты с некоторыми результатами наших предыдущих тестов (мы ведь писали выше, что публикуем не всё), видим совпадение веса снятого металла с точностью до десятых долей грамма, хотя предыдущий тест мы проводили два года назад. Да, некоторые круги из представленных здесь мы испытывали раньше, и такое совпадение служит для нас надёжным подтверждением справедливости выкладок.
Набор отобранных для теста кругов совсем не случаен. 3М Cubitron II – как представитель инновационного направления, «кубитрон» мы испытывали уже не раз. Зная, что этот тип абразивов требует мощного инструмента, было очень интересно посмотреть, что покажут слабенькие «болгарки». Кстати, это были круги толщиной 4 мм – универсальные, их можно применять и как зачистные, и как отрезные.
Bosch, причём двух серий, был выбран как пример абразивов, хорошо известных и популярных на российском рынке. Причём одна серия кругов – европейская (Словения), вторая – китайская.
Круги Abraflex мы взяли потому, что они попадались нам на глаза буквально при каждом выходе в Интернет. Похоже, компания инвестировала очень серьёзные суммы в контекстную рекламу. И к тому же мы ранее получали очень много вопросов от промышленных предприятий, знакомых с нашими тестами, именно по этим кругам. Раньше марка Abraflex в наших тестах не участвовала, и мы решили, что пора бы узнать, что это за продукт такой, к которому столько вопросов.
Правда, тут нам пришлось подумать, какие именно круги взять. Дело в том, что на рынке есть два вида кругов Abraflex – со знаком OSA и без него. Как нам известно, сейчас по этому поводу идёт разбирательство, OSA пытается выяснить, как на кругах оказался их логотип без необходимого в таком случае пятизначного цифрового кода. О правилах нанесения знака можно прочитать в интервью с представителями OSA. До появления официальной информации от OSA мы приняли решение считать круги Abraflex с соответствующим логотипом «сомнительными» и на тест взяли круги без знака.
OSA стандарт качества EN 12413 Eisenwarenmesse 2016
TOTFlex – круги российского производства, сделанные в Иваново, на «ИСМА», и не по обычному рецепту, а с амбициями на высокие результаты. Конкретно эта серия кругов, называемая Aggressor, содержит циркониевое зерно, что увеличивает производительность.
Сначала мы думали ограничиться этим набором. Но, обработав полученные результаты, поняли, что без кругов Лужского абразивного завода статья будет неполной. Ведь что делает тот снабженец, что стремится сэкономить? Очевидно, он покупает маломощную дешёвую УШМ и самые дешёвые круги к ней… то есть лужские. Так в нашей статье появилась ещё и продукция отечественного абразивного гиганта.
Теперь об инструменте. Для работы мы взяли три углошлифовальные машины Bosch – GWS 1000, GWS 1400 и GWS 19-125. Выбор обусловлен тем, что на момент подготовки статьи самой мощной УШМ на 125-й круг из тех, что есть на рынке, являлась именно GWS 19-125 (1,9 кВт). Логично было брать машины одного производителя, в идеале ещё и с минимальными конструктивными отличиями.
Каждым кругом мы шлифовали в течение 5 минут, после чего делали перерыв, чтобы заготовка успела остыть. После каждого подхода измеряли вес заготовки и вес круга, вычисляя, сколько он снял металла за эти 5 минут и сколько потерял сам.
Работа каждым кругом считалась оконченной либо через полчаса шлифовки (то есть после шести пятиминутных подходов), либо при падении веса круга до 100 г, если он изнашивался быстрее, чем за полчаса. При таком весе его диаметр падает настолько, что круг можно считать полностью изношенным. У других кругов, «переживших» получасовую эксплуатацию, остаточный ресурс ещё позволял продолжать работу, но он невелик, и мы для упрощения расчётов считаем такие круги тоже полностью изношенными. Принципиального влияния на конечный результат это допущение не оказывает.
В итоге по каждому кругу и по каждой УШМ мы получили две цифры: какое количество металла снял каждый круг за время своей «жизни» и сколько ему на это понадобилось времени. В статье мы приводим эти цифры на первых двух диаграммах. На первой – вес снятого металла, на второй – производительность в граммах в минуту. Всё, что мы публикуем дальше, – это расчёты, основанные на полученных результатах и некоторых допущениях.
ИСХОДНЫЕ ДАННЫЕ ДЛЯ РАСЧЁТОВ
Чтобы рассчитать стоимость эксплуатации УШМ разной мощности, нам необходимо зафиксировать некоторые параметры, иначе уравнение не будет иметь решения. Для примера рассмотрим производство, где УШМ используют для шлифовки сварного шва типа С2 (согласно ГОСТ 5264-80), толщина свариваемого металла (катет шва) – 8 мм. В этом случае общий вес шва длиной 1 метр, согласно ОСТ 24.940.02 (отраслевой стандарт, разработанный Иркутским заводом тяжёлого машиностроения им. Куйбышева, в котором определяется масса наплавленного металла погонного метра шва), составляет 286 г при ручной электродуговой сварке. Лишний вес примем за 15% – итого вес снимаемого металла при обработке 1 погонного метра сварного шва считаем равным 43 г.
И теперь, опираясь на эти цифры, посмотрим, в какие суммы обойдётся шлифовка сварного шва длиной 1 км.
НЕМНОГО СТАТИСТИКИ И ВПЕЧАТЛЕНИЙ
Насколько обоснованными можно считать полученные нами данные? Мы подсчитали статистику и выяснили, что при подготовке этой статьи мы потратили больше 20 часов только на шлифовку. Это суммарные данные от таймера, по которому мы отмеряли пятиминутные интервалы. То есть никаких обедов, перерывов – только работа, только хардкор! За эти 20 часов было снято почти 11 кг металла. У нас было достаточно времени, чтобы не просто набрать исчерпывающую статистику, но ещё и осознать, какие ощущения и эмоции вызывает работа «болгарками» разной мощности. Со всей уверенностью заявляем, что киловатт – это издевательство над рабочим. Конечно, когда речь идёт об обработке стали. У древесины или алюминия картина может быть другой. Круг «гладит» деталь, скорость съёма металла практически никакая, рабочему остаётся только стоять и поминать недобрым словом тех, кто заставил его работать неэффективным инструментом.
Приведём простую аналогию, чтобы было понятнее. Процесс шлифовки с помощью УШМ мощностью киловатт и меньше – это не более чем лёгкий петтинг. Настоящий секс начинается как минимум от полутора киловатт!
Обратите внимание: использованные в тесте круги 3М Cubitron II отличаются от всех остальных меньшей толщиной – 4 мм. Это универсальные круги, подходящие как для шлифовки, так и для резки. От более толстых 6-миллиметровых логично ожидать более высокого результата.
Остальные круги – в чистом виде шлифовальные, толщиной 6 или даже 7 (TOTFlex Aggressor ) мм.
И последнее – просуммируем расходы на оснастку и оплату труда. Смотрим на итоговую диаграмму. Напомним, что разница в стоимости «болгарок» мощностью 1000 и 1900 Вт составляет около 6500 рублей. Разница в суммарных расходах на оснастку и оплату труда почти во всех случаях оказалась выше. Таким образом, делаем вывод, что разница в стоимости инструментов окупается уже на том объёме работы, который мы взяли в качестве ориентира, – на шлифовке сварного шва общей длиной 1 км. То есть где-то за неделю работы, а то и меньше.
А теперь учтите, что мы вообще не рассматривали такой момент, как выход «болгарок» из строя по причине их перегрузки, хотя это вполне типичная ситуация. Рабочему выдают маломощный инструмент, который толком не снимает металл. Возникает естественное желание надавить посильнее, но мощности двигателя не хватает, чтобы работать с такой нагрузкой. Поэтому падают обороты (а значит, круги расходуются намного быстрее), а через какое-то время УШМ сгорает от перегрузки. А потом появляются отзывы в Интернете: «болгарки» такого-то бренда ненадёжные, они сразу же ломаются, никогда такие не покупайте. Мы уверены, что значительная часть подобных комментариев спровоцирована именно неправильным выбором инструмента, в первую очередь по мощности.
ВЫВОДЫ
Мы хоть и говорим, что результат теста был заранее предсказуем, но никогда не пытались посчитать стоимость эксплуатации УШМ разной мощности. Однако масштабы финансовых потерь, обусловленных «экономией», нас не просто удивили – шокировали.
Да, вы можете сэкономить несколько тысяч рублей на покупке инструмента, но сразу же начнёте «отстёгивать»: за дополнительное рабочее время (ведь производительность ниже), за повышенный расход кругов… И за ремонт сломанных «болгарок», конечно же. Так что у стремящихся к тотальной экономии закупщиков после публикации этих данных появится очень серьёзный повод обеспокоиться своими карьерными перспективами.